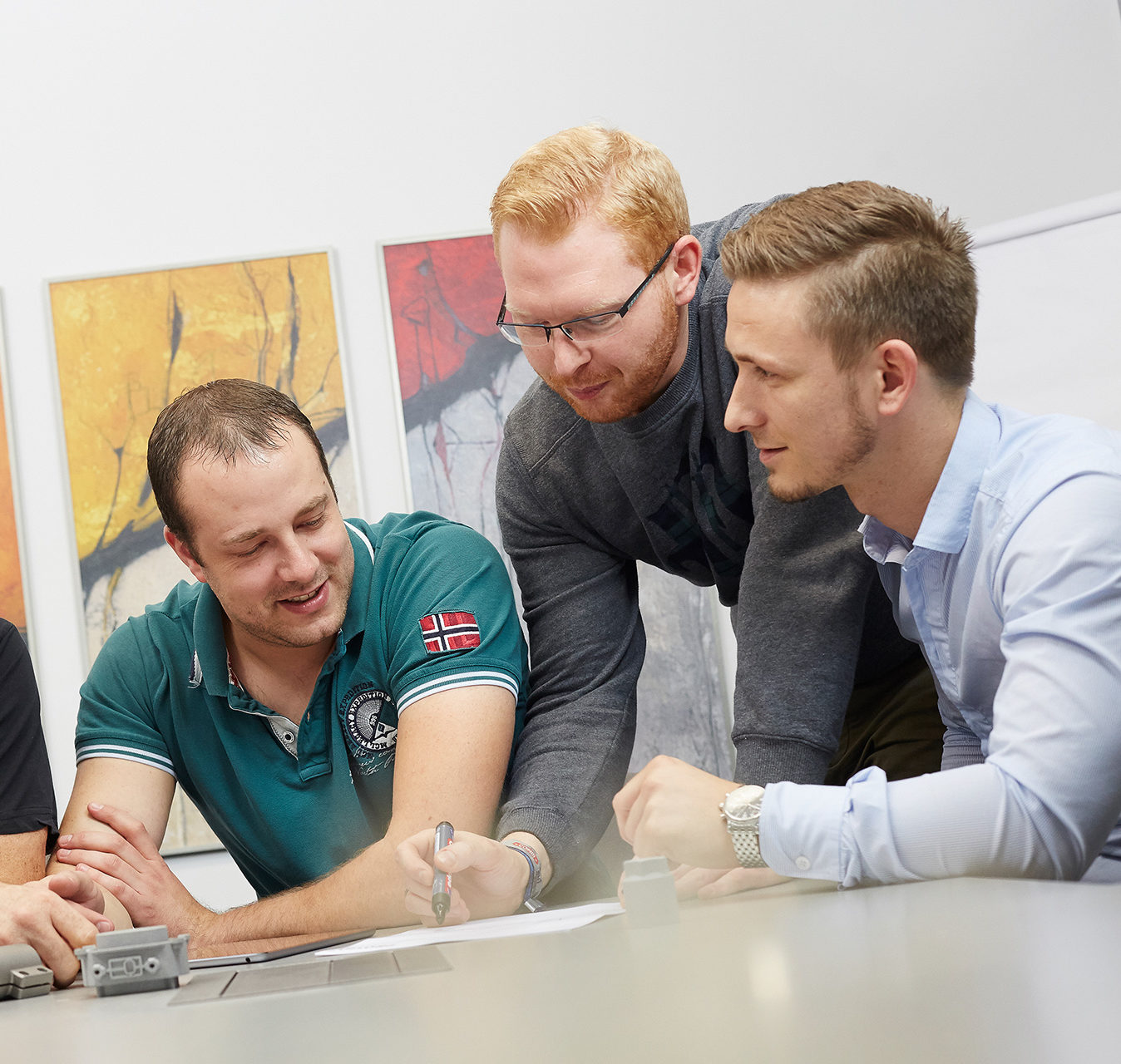
Keramik 3D-Druck
Keramik bildet neben Kunststoff und Metall eine weitere große Materialgruppe im 3D-Druck. Um aus Keramikpulver qualitativ hochwertige Objekte mit der materialtypischen hohen Dichte herstellen zu können, wir der Werkstoff in der additiven Fertigung in einem mehrstufigen Prozess verarbeitet. Zuerst wird im Stereolithographie-Verfahren aus einer flüssigen Keramik-Monomer-Suspension ein Grünkörper aufgebaut.
Zu diesem Zweck wird die Bauplatte in die Flüssigkeit abgesenkt und Schicht für Schicht auf Basis des vorliegenden CAD-Modells mit UV-Licht erhärtet. Um ein rein keramisches 3D-Objekt zu erhalten, werden dem Grünkörper im Anschluss die Polymer-Anteile durch Pyrolyse wieder entzogen. Diese werden lediglich als Binder benötigt, um das Werkstück vorrübergehend zu stabilisieren. In einem letzten Schritt durchläuft das 3D-Objekt schließlich einen Sintervorgang, um die keramischen Partikel zu verdichten.
Selektives Lasersintern (SLS)
Beim 3D-Druck-Verfahren selektives Lasersintern (SLS) werden pulverförmige Materialien aus thermoplastischen Kunststoffen aufgeschmolzen und zu funktionalen, mechanisch belastbaren 3D-Bauteilen aufgebaut, die häufig im industriellen Umfeld eingesetzt werden. Das Pulver wird mithilfe einer Rakel oder Rolle dünn auf eine bewegliche Bauplattform aufgetragen. Gemäß den Koordinaten aus dem vorliegenden CAD-Modell schmilzt ein Laser das Material an den entsprechenden Stellen auf. Anschließend senkt sich die Platte um den Wert genau einer Schichtdicke ab und der Prozess wiederholt sich bis zur Vollendung des Objekts. Das werkzeuglose Verfahren erlaubt sogar die gleichzeitige Herstellung mehrerer Fabrikate.
Das Material wird in der Baukammer bis kurz unter den Schmelzpunkt erhitzt, sodass bereits ein geringer Energieimpuls des Lasers ausreicht, um den Kunststoff aufzuschmelzen. Während des Bauprozesses wird das Werkstück vom umgebenden Pulverbett gestützt. Zusätzliche Supportstrukturen sind daher nicht notwendig – ein wesentlicher Vorteil, der große geometrische Freiheiten in der Konstruktion von 3D-Modellen gewährt.
Selektives Laserschmelzen (SLM)
Das selektive Laserschmelzen wird zur additiven Verarbeitung von Metallpulver verwendet und basiert auf demselben Verfahren wie das selektive Lasersintern. Ein leistungsstarker Laser schmilzt das Material mit hohen Temperaturen von bis zu 1.250 °C im Laserfokus auf. Durch große Temperaturunterschiede können unerwünschte Effekte wie Curling, Verzug oder Verbrennungen auftreten. Um einen optimalen Prozessablauf zu gewährleisten, wird deshalb eine Stützstruktur auf der Grundplatte mit aufgebaut, die das Werkstück stabilisiert. Diese muss im Anschluss manuell entfernt werden. Beim selektiven Laserschmelzen können viele verschiedene Metalle verarbeitet werden, zum Beispiel Edelstahl, Werkzeugstahl, Aluminium oder auch Kupfer. Letzteres ist aufgrund seiner außergewöhnlichen elektrischen und thermischen Leitfähigkeit ein wichtiger Werkstoff für die Industrie, die manuelle Verarbeitung durch Biegen und Löten ist jedoch äußerst zeit- und kostenintensiv. Der Einsatz intelligenter 3D-Druck-Technologie kann diesen Aufwand deutlich verringern und ermöglicht auf diese Weise eine wirtschaftliche Produktion bereits ab Losgröße 1. Im (Link einfügen) Induktoren Generator des PROTIQ Marketplace können hochleitfähige Kupferinduktoren nach individuellen Anforderungen online konfiguriert werden.
Stereolithographie (SLA)
Die vom Amerikaner Charles „Chuck“ Hull entwickelte Stereolithographie ist das älteste aller 3D-Druckverfahren. Mit ihr können in kürzester Zeit hochauflösende filigrane Bauteile aus Kunststoff produziert werden, weshalb die Technologie vor allem für das Rapid Prototyping verwendet wurde und wird. Als Ausgangsmaterial wird ein flüssiges Photopolymer (zum Beispiel Epoxidharz) verwendet. Der Kunststoff wird von einem UV-Laser Schicht für Schicht anhand CAD-basierter Koordinaten ausgehärtet. Im Anschluss an die Bestrahlung wird die Druckplattform um den Wert genau einer Schichtdicke in das Kunststoffbad abgesenkt, sodass die nächste Ebene mit der Flüssigkeit benetzt wird. Zwar wechselt der Werkstoff durch den Kontakt mit dem UV-Licht vom flüssigen in einen festen Zustand, stabil ist das Material jedoch noch nicht: Die vollständige Aushärtung erfolgt erst in einem finalen Schritt, in dem das Bauteil durch UV-Strahlung erneut bestrahlt wird. Eine Nachbearbeitung ist in der Regel nicht notwendig, da die Oberfläche der Objekte von vorn herein sehr glatt ist.
PolyJet/MultiJet Modeling (PJM/MJM)
Das PolyJet Modeling kommt dem herkömmlichen Tintenstrahldruck von allen 3D-Druck-Verfahren am nächsten. Der Druckkopf bewegt sich zügig über die Bauplattform und versprüht feine Tröpfchen eines flüssigen Polymers. Dabei wird das Material beinahe zeitgleich mit UV-Licht bestrahlt und so direkt ausgehärtet. Neben einer Vielzahl vollständig aushärtender Kunststoffe werden beim PolyJet-3D-Druck auch wachsartige Materialien verwendet, die ein zusätzlicher Druckkopf zu Stützstrukturen für das 3D-Objekt aufbaut. Diese werden im Anschluss an den Druckprozess manuell entfernt. Durch den Einsatz von mehr als zwei Druckköpfen entstehen außerdem Bauteile, die aus mehreren Farben oder sogar unterschiedlichen Materialien bestehen können – ein großer Vorteil für die Herstellung komplexer Funktionsprototypen und Anschauungsmodelle.